(di R. Petruzzelli) La prefabbricazione è il termine generale con il quale ci si riferisce a qualsiasi componente fabbricato in luogo differente dal sito ultimo di collocazione. Con riferimento al settore edilizio, si intende la realizzazione fuori opera di elementi, componenti edilizi e/o sottosistemi degli edifici.
Questi forgiati in fabbrica, in un ambiente altamente controllato grazie all’impiego di macchinari tecnologicamente settati e soggetti a continue verifiche, rispettano le prestazioni predefinite in fase progettuale e sono pronti per poter esser assemblati in fabbrica oppure trasportati nel sito di installazione dove seguiranno le fasi di montaggio.
>> Vorresti ricever approfondimenti come questo? Clicca qui, è gratis
Le potenzialità della prefabbricazione
Tanto premesso è possibile delineare le seguenti potenzialità della prefabbricazione e di conseguenza del sistema costruttivo a secco:
- sostenibilità ambientale: la progettazione e l’impiego di connessioni e giunzioni a freddo limitano al minimo l’uso di sostanze chimiche come collanti e resine ed evitano l’uso di malte il cui confezionamento richiede un consistente quantitativo di acqua e quindi un consumo di risorse.
Altresì, l’assemblaggio e il disassemblaggio delle strutture prefabbricate modulari in fabbrica o in loco riduce notevolmente i rifiuti tradizionalmente prodotti in cantiere con conseguente semplificazione delle fasi di differenziazione dei rifiuti nonché di riciclaggio dei materiali e riuso dei componenti. Tale contributo, a vantaggio del rispetto dell’ambiente, si avvalora grazie alla versatilità del modulo, dal momento che lo stesso può esser adattato per rispondere a diverse esigenze durante il suo ciclo di vita; - velocita di realizzazione: i tempi di realizzazione rispetto alle architetture tradizionali sono brevi in quanto le aziende produttrici forniscono una gamma di moduli con formula “chiavi in mano”. Si tratta di moduli completi e funzionanti, dotati di ogni finitura e di impianti già installati. I tempi che intercorrono dalla produzione alla fruizione, in questo caso, dipendono solo dal trasporto dal deposito/azienda al sito e dai tempi di assemblaggio qualora siano previsti più moduli per la definizione spaziale;
- flessibilità: caratteristica intrinseca dovuta al poter aggiungere, sottrarre e modificare i componenti dei moduli dando vita a spazi altamente flessibili che rispondono alle esigenze specifiche di ciascuna committenza;
- facilità di trasporto: le dimensioni predeterminate consentono il trasporto su mezzi ordinari come navi ed autogru di moduli assemblati nella loro configurazione spaziale o trasportati in modalità flat pack. In questo caso, ogni modulo è disassemblato nelle sue componenti, in particolar modo il basamento e la copertura diventano elementi dell’imballo, all’interno del quale vengono inseriti tutti gli elementi impiantistici, strutturali e non, con i componenti necessari al montaggio. Questo sistema di trasporto consente una riduzione dei volumi e la possibilità di non effettuare il trasporto eccezionale con conseguente aumento dei costi;
- gestibilità: La composizione della stratificazione a secco per la sua facilità e scomponibilità è orientata all’ottimizzazione dei tempi e delle fasi di manutenzione. Nel ciclo di vita della struttura, infatti è possibile rimuovere o effettuare il ripristino di un componente senza la necessità di intaccare altre porzioni costituenti il manufatto. La rapidità dell’intervento localizzato, garantisce la lo svolgimento delle attività negli spazi senza particolari interruzioni.
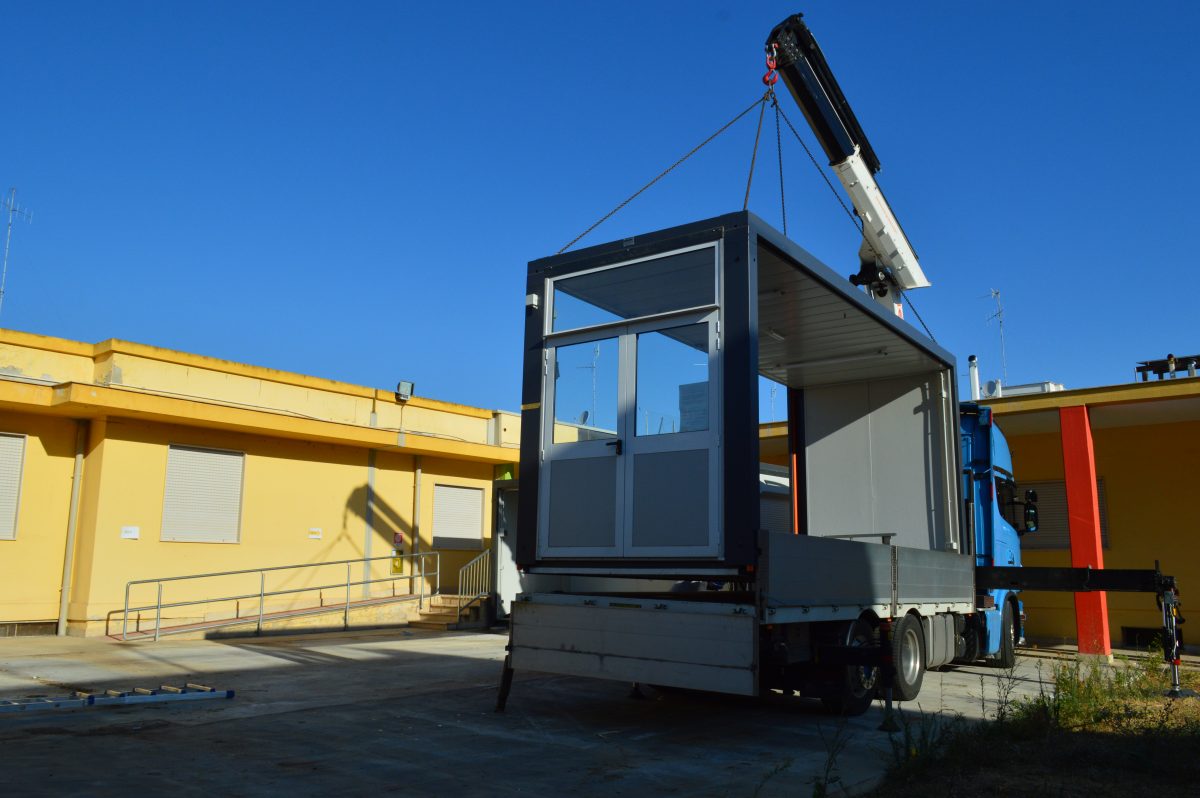
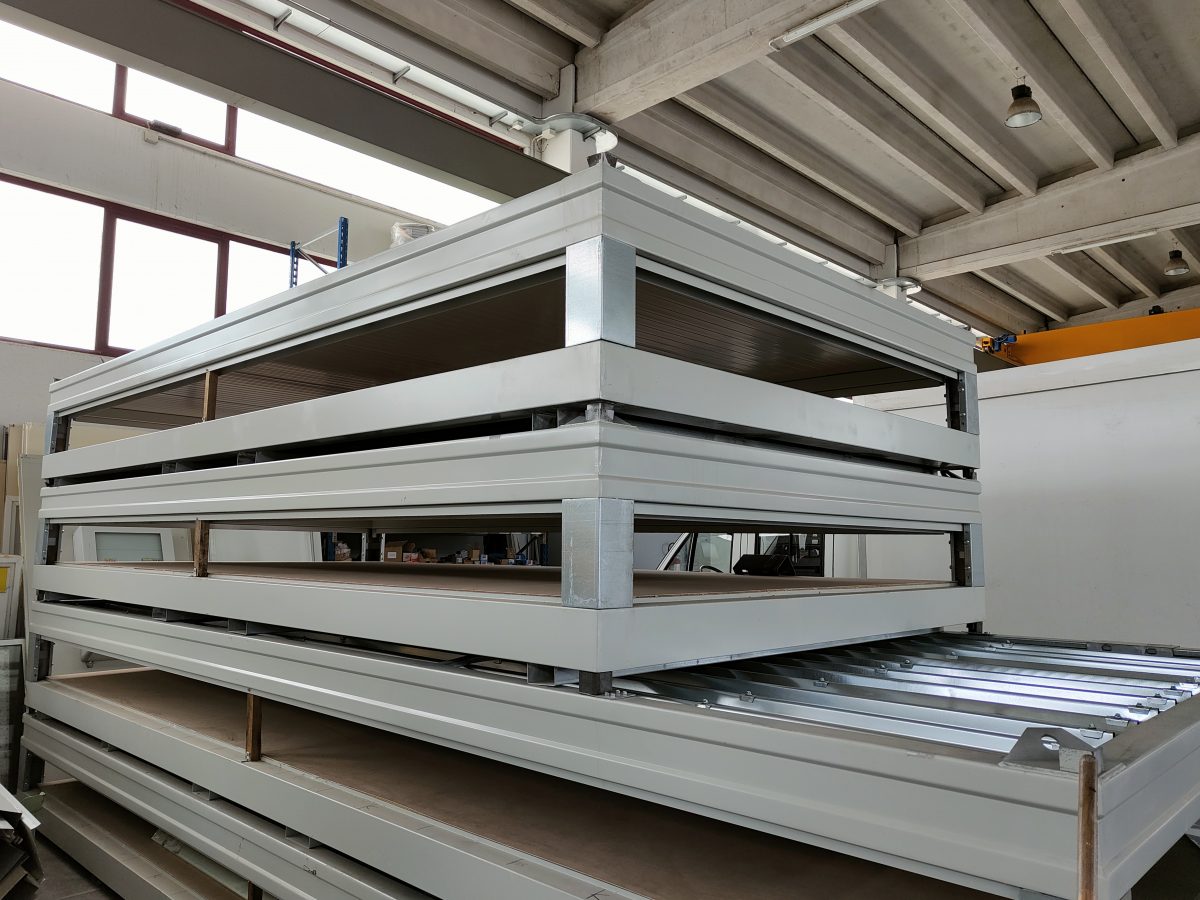
Potrebbe interessarti: Fondazioni edifici prefabbricati. Quali accorgimenti seguire per calcolo e verifica?
I gradi della prefabbricazione e la definizione dimensionale del modulo
La costruzione stratificata a secco è frutto della giustapposizione di diversi componenti, con diversi gradi di complessità e specializzazione. Si utilizzano, infatti, profili di supporto, pannelli e stratificazioni di materiali isolanti che nel complesso definiscono il manufatto.
L’avvio di un processo di progettazione necessita a monte della scelta del grado di fabbricazione che si vuole adottare per poter meglio valutare il rapporto di convenienza fra le prestazioni offerte dai componenti prefabbricati e quelle complessive del sistema. In generale, con grado di prefabbricazione si intende la complessità e le dimensioni dei componenti prefabbricati che portano alla configurazione finale del prodotto.
Si possono distinguere quattro gradi di prefabbricazione:
- i materiali: colonne e travi di diverso materiale come legno o acciaio;
- i componenti: singoli elementi come scale, infissi la cui messa in opera richiede particolare attenzione alle connessioni, agli allineamenti e ai controlli di stabilità;
- i pannelli, sistemi 2D: elementi bidimensionali, il cui grado di prefabbricazione è di circa il 60 %, utilizzati per realizzare pareti strutturali, solai e coperture;
- i moduli, sistemi 3D: noti anche con il termine di PPVC (Prefabricated Prefinished Volumetric Construction) sono unità strutturali tridimensionali, il cui grado di prefabbricazione sale fino all’85%, o nel caso di presenza di finiture interne anche al 95%.
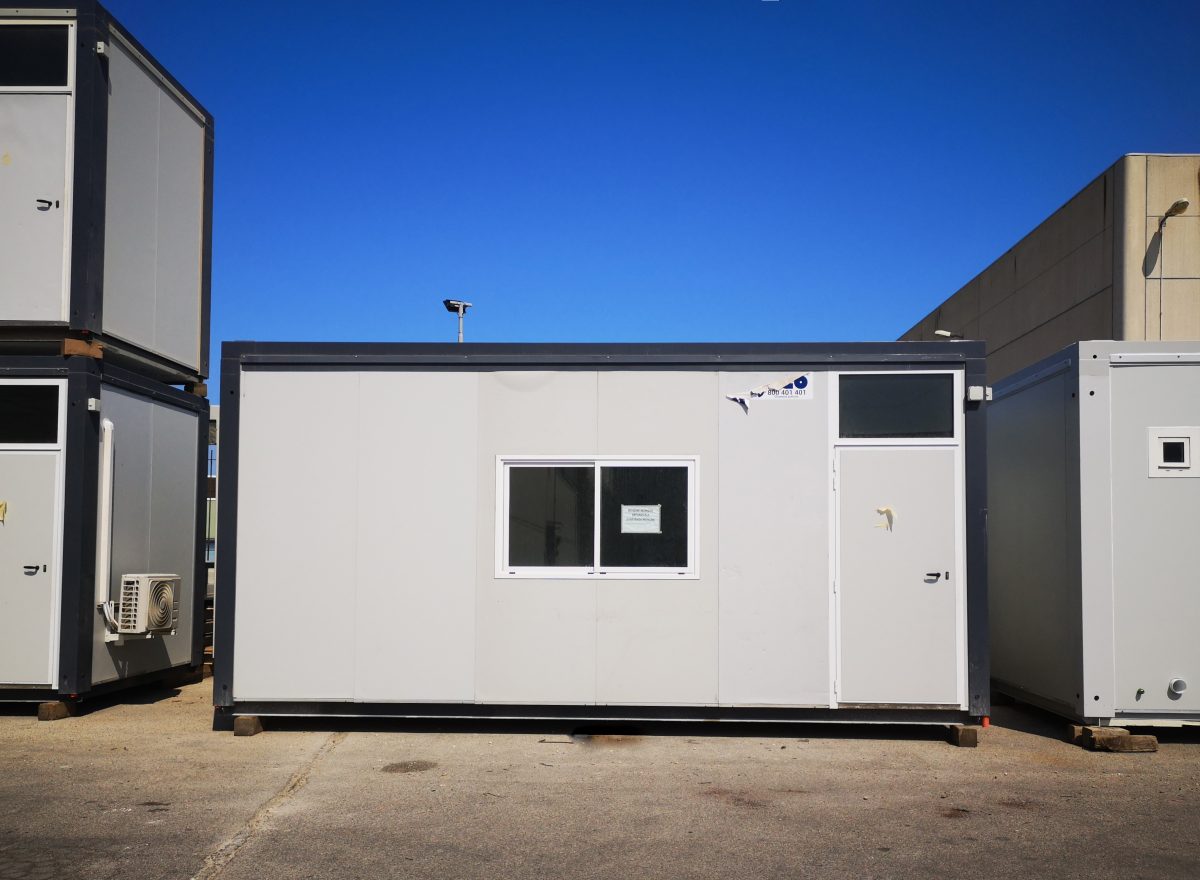
Generalmente la costruzione fuori sito adotta un sistema unico o un sistema ibrido, combinando i diversi gradi di prefabbricazione. La definizione delle dimensioni dei moduli prevede il richiamo agli standard definiti dall’International Organization for Standarization (ISO). In particolare, la norma ISO 668:2020 specifica le dimensioni dei container, le funzionalità, le applicazioni e i limiti strutturali. Il rispetto delle dimensioni limite definite dalla suddetta, consente la facilità di trasporto con appositi mezzi ordinari.
Potrebbe interessarti: Strategie di manutenzione ed estensione della vita utile di ponti e viadotti
Di seguito, si riportano le dimensioni standard dei container più utilizzati in ambito edilizio:
- container ISO 20’ con dimensioni esterne: larghezza pari a 2,438 m, lunghezza di 6,058 m ed un’altezza massima di 2,896 m;
- i container ISO 40’ con dimensioni esterne: larghezza 2,438 m, lunghezza 12,192 m ed altezza massima pari a 2,896 m.
Le dimensioni dei container sono tali, come accennato, da poter consentire il trasporto su autoarticolati ma è necessario notare che l’altezza massima risulta esser pari a 2,896 metri. In relazione alle suddette dimensioni, le gamme di moduli presenti sul mercato hanno un’altezza minima di 2,20 m, alla quale segue 2,50 m e 2,70 m. Per questi valori, il trasporto può esser effettuato su autocarri dotati di gru per il sollevamento e posizionamento dei moduli, rispettando i valori limiti imposti dal Codice della strada.
Qualora la dimensione dei moduli supera i 2,70 m, il trasporto diventa un trasporto eccezionale, cosi come definito all’art. 61, comma 6 del Codice della strada. Questo è il caso delle unità base aventi una destinazione d’uso scolastica, per i quali l’altezza minima interna è fissata a 3,00 m, ai sensi del decreto ministeriale 18 dicembre 1975, salvo deroghe. L’effettuazione di un trasporto eccezionale comporta un maggiore onere che incide sul costo complessivo della realizzazione, per tale ragione le aziende possono ricorrere alla modalità flat pack.
L’articolo è di Rosa Petruzelli, building engineer presso l’Azienda Algeco. Da sempre appassionata di progettazione e costruzione, affronta ogni nuovo progetto con entusiasmo puntando alla ricerca della soluzione efficiente. La sua spiccata curiosità e determinazione la conducono ad esplorare nuove culture e settori perché convinta che la ricchezza risieda nella conoscenza.
Scrivi un commento
Accedi per poter inserire un commento